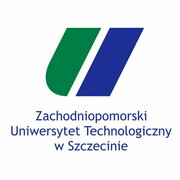
Jednostki naukowe: Zachodniopomorski Uniwersytet Technologiczny w Szczecinie
Poziom gotowości technologicznej (TRL): 7
Rozwiązanie dotyczy urządzenia mechatronicznego do montażu przyłbic ochronnych dla pracowników służby zdrowia i innych osób udzielających pierwszej pomocy medycznej. Urządzenie to będzie pracować w trybach półautomatycznym lub automatycznym z wykorzystaniem łatwo dostępnych półfabrykatów, bez udziału człowieka w procesach montażu. Urządzenie będzie efektem powiązania nowatorskiej konstrukcji z systemem sterowania czasu rzeczywistego, umożliwiającym swobodne przeprogramowywanie oraz zdalne zarządzanie procesem produkcyjnym.
Materiał Szczecinbiznes.pl - http://szczecinbiznes.pl/prezentacje/Automat-do-produkcji-przylbic_5775
Wzór przyłbicy zaplanowany do montażu w projektowanym urządzeniu jest dopasowany do skali problemu COVID. Przyłbice te, wykonane z łatwo dostępnych elementów: folii ochronnej, taśmy mocującej i spinki są lekkie, wygodne, nie utrudniają ruchów i chronią przed kropelkami. Poprawiają więc zdecydowanie komfort i jakość pracy personelu medycznego. Są ponadto tanie w produkcji (szacowany koszt 0,50 PLN/szt.) i tak samo będą konkurencyjne cenowo. W normalnym okresie przyłbica techniczna kosztowała ok. 25-30 zł. obecnie w granicach 40-50 zł. W związku z tym, zaplanowane do wytwarzania przyłbice mogłyby być używane jako jednorazowe środki ochrony osobistej, co ma duże znaczenie szczególnie dla pracowników ochrony zdrowia. Warto jednak nadmienić, że przyłbica ochronna po użyciu nie musi być wyrzucana (można ją dezynfekować) co powoduje, że wynik projektu nie będzie negatywnie oddziaływał na środowisko naturalne w regionie czy też kraju.
Ważnym aspektem jest również sposób produkcji przyłbic ochronnych, wykonywanych w zdecydowanej większości w sposób ręczny z elementów termoplastycznych. Polega to na wycinaniu elementów z wypraski, składaniu i łączeniu z arkuszem z poliwęglanu, a następnie pakowaniu. Zwykle wygląda to tak, że w hali produkcyjnej pracuje kilkadziesiąt osób, które składają produkt, co zwiększa możliwość wzajemnego zarażenia się pracowników i rozprzestrzeniania epidemii. W odróżnieniu od montażu ręcznego, automat może pracować non stop w komorze o kontrolowanym środowisku, umożliwiającym ewentualną dekontaminację.
Maszynę/kilka maszyn może obsługiwać jeden operator, odpowiednio zabezpieczony. Występuje więc śladowe ryzyko zakażenia wśród pracowników. Automatyzacja procesu wytwarzania przyłbic ochronnych z łatwo dostępnych i tanich półproduktów umożliwia ponadto uniezależnienie się od dostaw zewnętrznych, co było szczególnie odczuwalne na pierwszych tygodniach stanu pandemii.
Podsumowując, oferowana technologia wydatnie poprawi jakość życia i zdrowia mieszkańców, dostarczając personelowi medycznemu (lekarzom, pielęgniarkom, ratownikom medycznym itp.) dużych ilości środków podstawowej ochrony medycznej. Nie będą oni dzięki temu borykali się z podstawowymi problemami w dostępności takich środków, jak to miało miejsce podczas pierwszych tygodni pandemii, co wpłynie na ich komfort pracy i w rezultacie – jakość usług medycznych. Odnośnie korzyści gospodarczych, możliwość uruchomienia zautomatyzowanej produkcji przyłbic spowoduje z pewnością zainteresowanie innych jednostek medycznych nie tylko z regionu, co wprost przełoży się na zwiększenie aktywności gospodarczej regionu.
Skonstruowanie urządzenia do automatycznego wytwarzania przyłbic ochronnych, zgodnie z autorskim projektem wzorniczym, będzie wpływało na walkę ze skutkami wystąpienia COVID-19 wieloaspektowo:
a) poprawa dostępności tego typu środków ochrony osobistej, ze względu na planowaną wysoką wydajność urządzenia – dzięki zautomatyzowanemu procesowi produkcji przyłbic, będzie można dostarczyć je na rynek szybciej oraz z większych ilościach, co wydatnie poprawi wydajność regionalnej oraz krajowej służby zdrowia,
b) pozytywny wpływ na wzrost bezpieczeństwa wytwarzania przyłbic, poprzez minimalizację liczby osób zaangażowanych w montaż. Jak opisano w innych częściach wniosku, obecnie montaż przyłbic wykonywany jest ręcznie przez duże zespoły ludzkie, które zgromadzone w jednym miejscu (nawet w przepisowych od siebie odległościach) wydatnie zwiększają szansę na wzajemne zarażanie się wirusem. Wykrycie wirusa u członka takiego zespołu może skutkować w najlepszym razie zmniejszenie wydajności ręcznego składania przyłbic (wysłanie chorego członka zespołu na kwarantannę), a w najgorszym razie – zaprzestanie składania przyłbic (izolacja całego zespołu). Oferowane urządzenie rozwiązuje ten problem.
Maszyna pomaga w złożeniu na życzenie przyłbicy z łatwo dostępnych materiałów, co jest szczególnie kluczowe w sytuacjach kryzysowych, gdy takich zasobów brakuje, przy równoczesnym zmniejszeniu kosztu przyłbicy. Równocześnie złożenie przyłbicy ułatwia przetrzymywanie zasobów (złożona przyłbica zajmuje dużo miejsca i przetrzymywanie dużej ilości może powodować uszkodzenia)
Skala stosowania wyniku projektu będzie masowa – urządzenie może być wykorzystywane na terenie całego kraju, możliwości skalowania produkcji w ten sposób są również bardzo szerokie. Z całą pewnością można stwierdzić, że potencjalne oddziaływanie technologii jest zdecydowanie większe niż tylko poziom regionalny.
Montaż przyłbic ochronnych w dostępnych wzorach jest prowadzony w sposób ręczny. Urządzenie do automatycznego montażu przyłbic ochronnych zgodnie z oryginalnym wzorem stanowi innowację produktową na poziomie co najmniej regionalnym i krajowym. Urządzenie wg. projektu pozwoli na zautomatyzowanie procesu wytwarzania przyłbic ochronnych z łatwo dostępnych komponentów.
Główna innowacyjność polega na automatyzacji procesu składania przyłbic i tym samym poprawie wydajności tego procesu, która to wydajność jest jednym z kluczowych elementów przeciwdziałania rozprzestrzeniania się wirusa – obecnie nie znane są na terenie regionu oraz kraju maszyny tego typu.
Oferowana technologia została sfinansowana ze środków Regionalnego Programu Operacyjnego Województwa Zachodniopomorskiego 2014-2020, w ramach realizacji projektu „Odpowiedzialny społecznie Proto_lab”.
Zgodnie z wytycznymi projektu, komercjalizacja polega na udzieleniu licencji niewyłącznej na przedstawianą technologię, na następujących warunkach:
- opłata wstępna: 1000 zł netto, płatna w terminie 14 dni od podpisania umowy licencji
- opłata licencyjna: 6,40% od przychodu ze sprzedaży produktów lub usług wyprodukowanych na bazie oferowanej technologii.
Kontakt z Brokerem Technologii
Regionalne Centrum Innowacji i Transferu Technologii, Zachodniopomorski Uniwersytet Technologiczny w Szczecinie
Daria Wróbel
tel. 725 29 28 08
e-mail: dwrobel@zut.edu.pl